
Bow Thruster Installation: Why choose a Sleipner Thruster?
Built for outstanding performance, you can rely on your Sleipner bow thruster or stern thuster year after year. Boat builders all over the world are choosing Sleipner for reliability, ease of installation and unrivalled safety features.
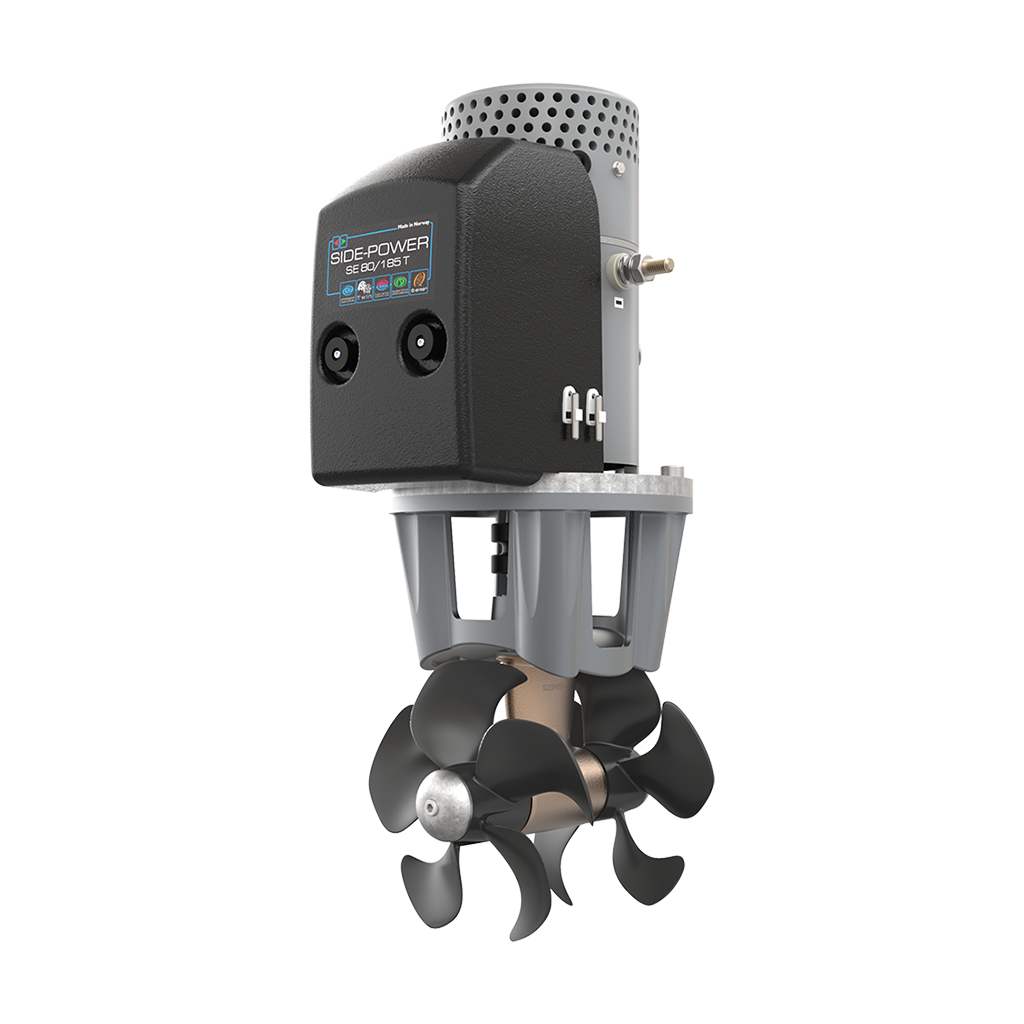
Side-Power SE80 thruster
Sleipner thruster performance
The high performance of a Sleipner thruster is the result of years of development and testing.
- Propulsion technology know-how
- 5 bladed composite propellers
- Purpose-built high power electric motors
- Improved waterflow from streamlined gearhouse design
Installation of Sleipner thrusters
Through our extensive experience and close co-operation with major boatbuilders we know how important a correct installation is for the thruster system. Therefore we have made all the preparations to ensure that it is easy to install a Side-Power thruster correctly.
- Compact-sized units
- “Plug and go” electric wiring
- Easily accessible battery cable terminals
- Fast and safe propeller mounting with locknut
- Professional and solid GRP stern thruster kits
- Easy access zinc anodes
Safety Features of Sleipner thrusters
- No overheating of electric motor
- Mechanical protection of drive gear
- Electronic protection against sudden change of drive direction
- No accidental operation from child safe on/off and automatic deactivation
- Selvslukkende reledeksler
- IPC comes standard on all DC electric thrusters reducing solenoid wear and the risk of lock in.
- Production, assembly and quality control taking place in our ISO-certified factory in Fredrikstad, Norway
Guide to Sleipner Thruster Technology
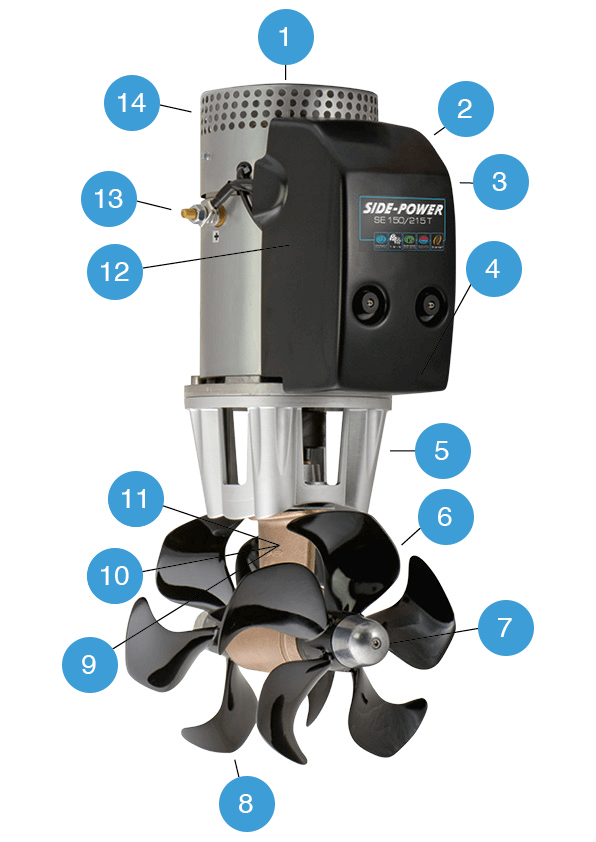
Key to Sleipner thruster technology
1: Electric motor developed by Sleipner for maximum performance and efficiency.
2: Contactors developed by Sleipner for extended main solenoid lifetime.
3: Patented IPC system monitoring solenoids to reduce chance of solenoid lock-in, stops thruster in case of malfunction.
4: Automatic delay between change in drive direction to protect motor and gearleg.
5: Gearleg galvanically separated from electro motor to protect immersed parts from accidental short circuit or current leaks.
6: Compact streamlined gearleg minimises water resistance and reduces cavitation.
7: Anodes outside propellers for easy replacement.
8: Composite Q-Prop propellers for maximum efficiency and minimal noise.
9: CNC-machined and assembled to perfect tolerances.
10: Hardened spiral-cut gears for extended lifetime, low noise and more compact gearleg design.
11: Pre-filled gear-leg for easy installation and less maintenance. High quality oil for extended lifetime.
12: Closed solenoids to prevent dust and pollution on contacts.
13: Easily accessible power terminals.
14: Thermal switch prevents overheating.
Leave a Reply
You must be logged in to post a comment.