
Sleipner Thruster Trouble-Shooting Guide
Trouble-Shooting Guide for post-2005 Thrusters with IPC Control System
Recommended Tools For Trouble-Shooting
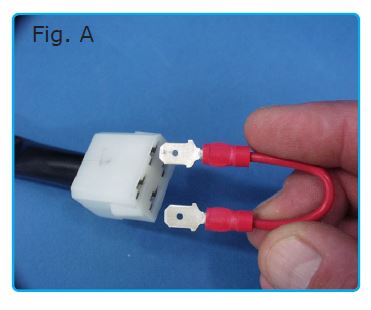
• Metric Allen Wrenches, 4mm to 12 mm
• Metric wrenches or sockets
• Needle Nose Vise-Grips
(for holding jammed nuts when removing battery cables from motor)
• Phillips head screwdriver
• Small jumper wire
(with male quick discontent terminals if available, (Fig. A)
• 12” jumper wire with alligator clips
• Multi-meter (with alligator clips if available)
Identifying Thruster Parts…
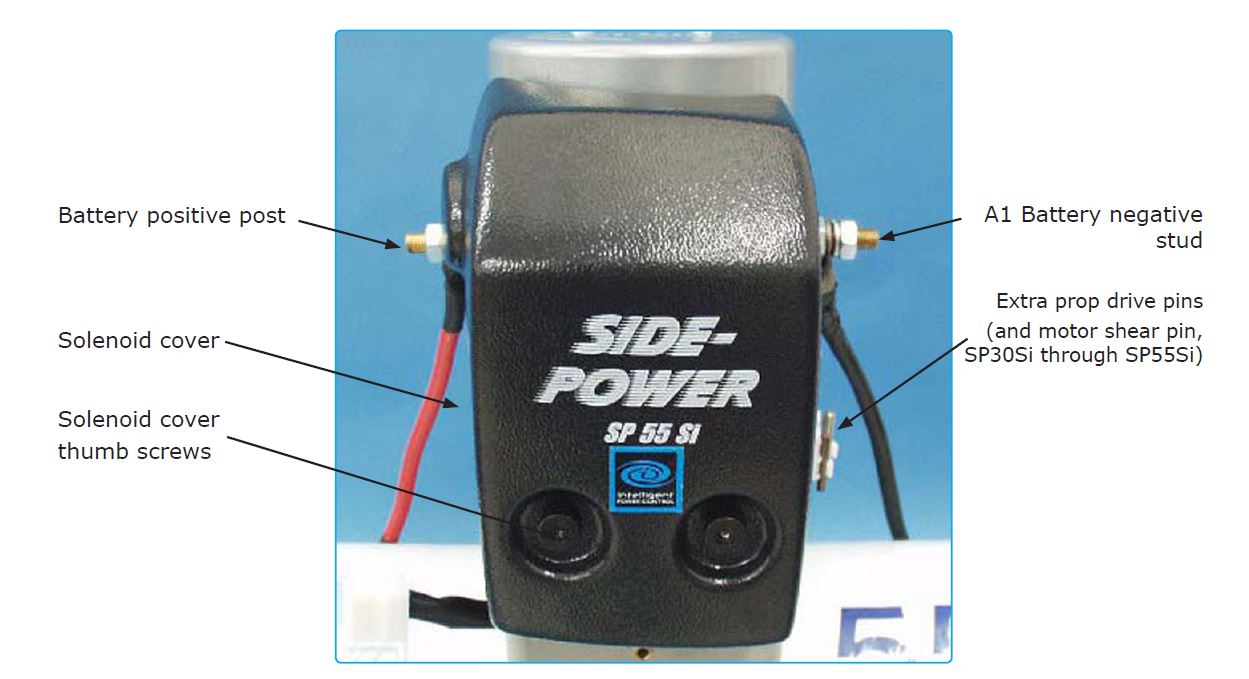
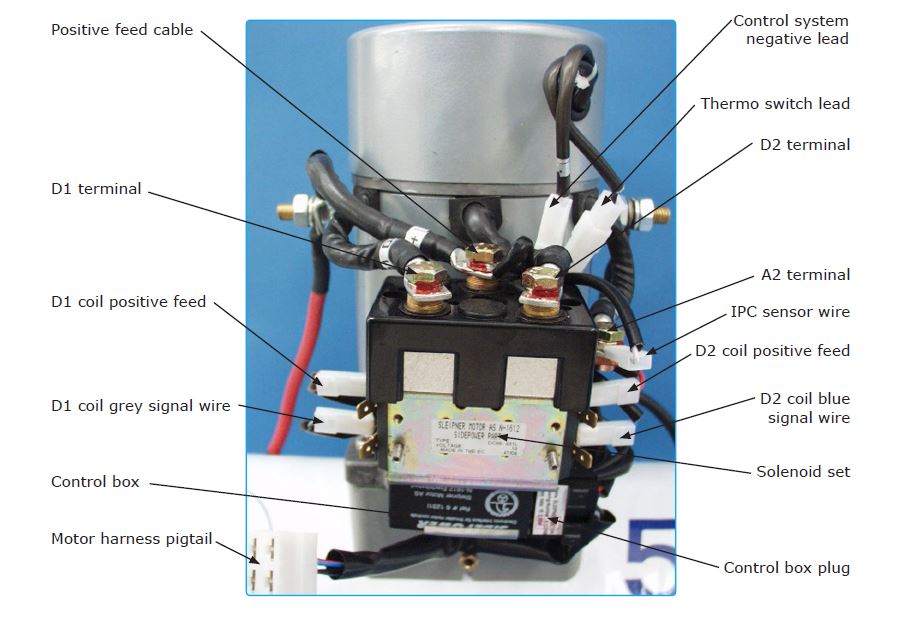
If Control Panel Does Not Turn On…
1. Check battery power
The control panel is powered through the bow thruster. The thruster is usually on its own circuit, meaning the positive and negative battery cables run directly between the thruster and the battery. A fuse should be installed on the positive cable within 72” of the battery. Check that it is not blown. A battery switch is usually installed in close proximity to the fuse and battery. Check that the battery switch is turned on.
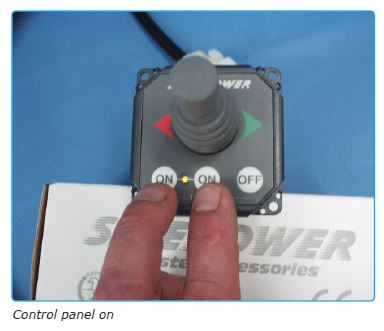
2. Check Voltage At The Thruster
You should read battery voltage at the thruster. If there is no voltage at the thruster, there is a problem with the power supply. Check the battery, fuse, switch, and cabling.
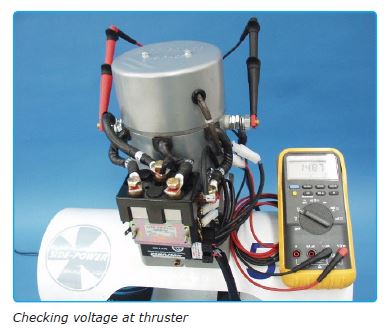
3. Check for Voltage on the Control Harness Pigtail
With multi-meter set to DC volts, check from red wire (positive) to black wire (negative) on motor wiring harness pigtail. If there is battery voltage at the thruster battery cables, but no voltage at the motor harness pigtail, than proceed to step 4.
If there is battery voltage on the motor control harness, repeat step 3 on control harness at the control panel to ensure there is no fault with the control harness run. If there is battery voltage at control panel then there is a problem with the control panel. Please contact your local Side-Power distributor for service support.
Check Control System Positive and Negative
• Check for voltage between the battery negative stud and red wire on motor harness pigtail.
• If no voltage is present, then check that all motor harness and control box plug connections are tight and in place. If the motor harness checks out, then there may be a problem with the control box. Please contact your local Side-Power distributor for service support.
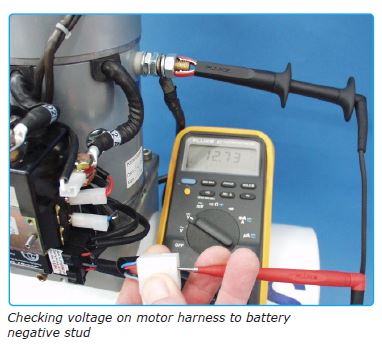
If voltage is present, locate the control system negative lead and unplug it from the motor harness. With multi-meter set on ohm (O), check for continuity between the control system negative lead and the A1 battery negative stud. There should be continuity; ohms will go close to 0 (usually about 0.2O-0.5O).
If there is no continuity between the control system negative lead and battery negative stud, then please contact your local Side-Power distributor for service support.
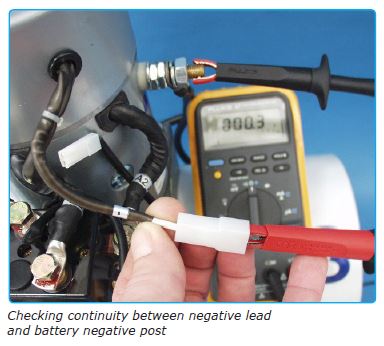
If there is continuity between negative lead and battery negative stud, reconnect control system ground lead to motor harness, then check for continuity between the black wire on the motor harness pigtail and battery negative stud. Set the multi-meter on diode-test position, showing about 0.5V-0.7V. (A diode is fitted on the black wire).
NB: Be sure to have positive lead connected to motor pigtail and negative lead to control box plug
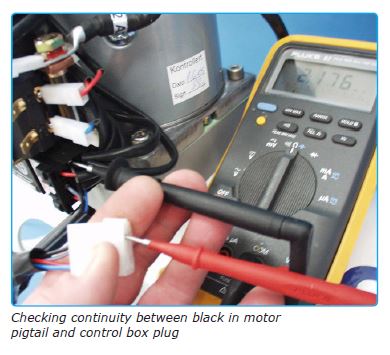
If there is no continuity between these two points than the motor harness has been damaged.
If Control Panel Does Not Turn On But Thruster Does Not Run, Or Thruster Runs In One Direction Only
NB: The preceding tests are to be performed while the boat is in the water. Please contact us for service support on 01603 784884
1. Bypass Control Panel and Check Thruster Control Box and Solenoid Operation
Remove control panel and unplug wiring harness or unplug control harness from motor harness pigtail, whichever is more convenient. On the four wire Amp connector (wiring harness if disconnected at control panel or motor pigtail if disconnected at motor), with short jumper wire, jump from red to blue for starboard run, and red to grey for port run.
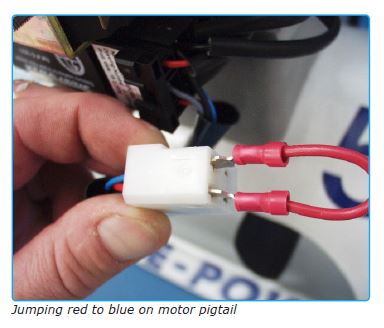
NB: Be careful not to jump red to black as this will PERMANENTLY DAMAGE THE CONTROL BOX
If thruster runs in both directions when jumping red to blue and red to grey on the motor harness pigtail, repeat this test on the control panel’s harness at the control panel. If the thruster runs, then the control panel is likely damaged.
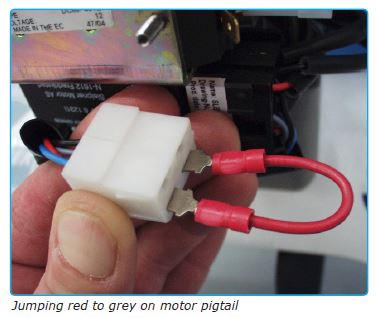
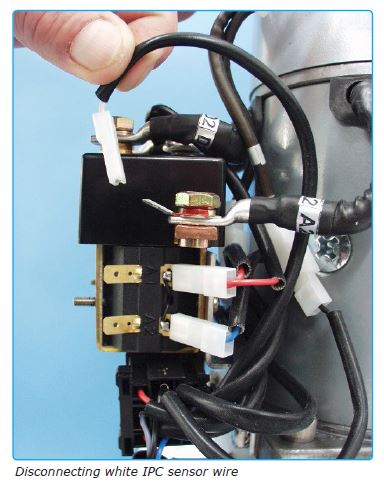
If the thruster does not run, or runs in only one direction, at the control panel, but runs in both directions at the motor harness pigtail, then the harness or terminals are damaged.
NB: Be sure that all control panels in the system are unplugged when doing this test
If thruster does NOT RUN – proceed to Step 2.
2. Bypass thruster control box and check thruster solenoid operation
Disconnect the white IPC Sensor wire on the A2 Terminal.
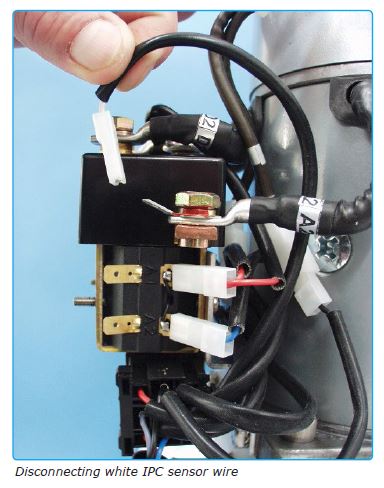
With long jumper wire, jump from negative battery stud to D1 coil grey signal wire for port run, and to D2 coil blue signal wire for starboard run.
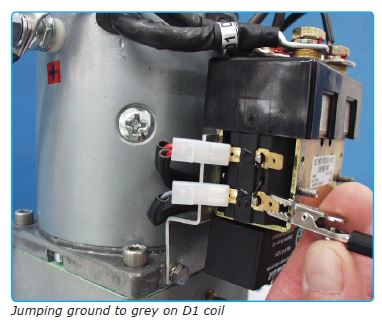
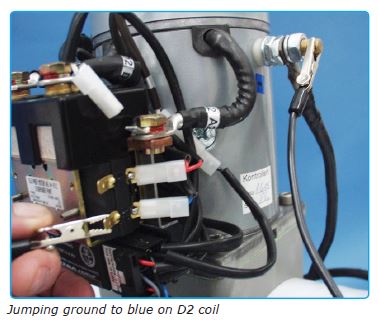
If thruster runs properly, proceed to Step 3
If thruster does not run, proceed to Step 4
3. Checking The Thermo Switch
Locate the thermo switch lead and unplug it from the motor harness. With multi-meter set on ohm (O), check for continuity between the thermo switch lead and the battery negative stud. There should be continuity; ohms will go close to 0 (usually about 0.2O -0.5O).
If there is no continuity between thermo switch lead and A1 battery negative stud, then either the thermo switch needs to be replaced or the A1 battery negative stud has been damaged internally. Verify that the A1 Battery negative stud is OK by checking for continuity between A1 and A2. If there is continuity then the A1 battery negative stud is OK.
If there is continuity between thermo switch lead and battery negative stud then there is a problem with the control box or the motor wiring harness. Please contact your local Side-Power distributor for service support.
4. Check for solenoid output
With jumper wire still attached and IPC wiredetached from step 2, check for voltage on the A2 terminal.
If no voltage is present on A2 terminal then the solenoid pack may need to be replaced. Please contact your local Side-Power distributor for service support.
If voltage is present on A2 terminal then the motor may be damaged. Please contact Your local Side-Power distributor for service support.
5. Check the Operating Voltage
Once the thruster is operating properly, check the voltage between the battery positive post and the battery negative post while the thruster is running. The voltage will drop initially and then should level off after approximately 5-10 seconds.
The voltage should be no lower than 9.5 for a 12 volt thruster and 19 volts for a 24 volt thruster after the voltage has stabilized.
If the voltage does not stabilize and continues to drop below 9.5 or stabilizes below 9.5 for 12 volt thrusters (19 volts for 24 volt thrusters), then the battery source needs to be checked to ensure that the amp capacity is sufficient to run the thruster. The cable run also needs to be checked, for voltage drop.
Please contact your local Side-Power distributor for service support if you have low operating voltage.
Leave a Reply
You must be logged in to post a comment.